Challenging the Myths of Battery-Powered Aviation
Shourya Bhandari, Leonardo Times Editor
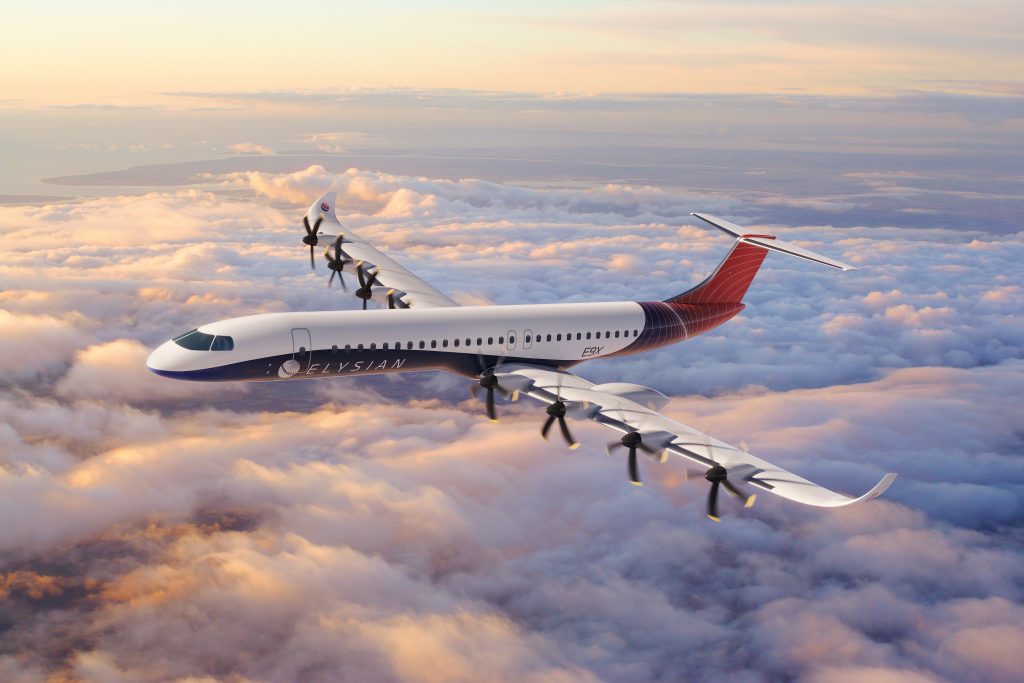
The E9X designed by Elysian Aircraft promises to be a more sustainable approach to reducing CO2 emissions produced in commercial aviation by providing a battery-electric alternative to more than 50% of scheduled commercial flights [1]. Promising to lower operational costs for airlines while also being the most efficient path to zero-emission travel compared to other fuel sources, this new aircraft could be the innovation needed to meet the EU’s net-zero carbon emission goal by 2050 [2].
The Elysian project commenced in 2021 and became a private venture in 2023. Their initial efforts were condensed into a series of ground-breaking papers released to the public at the 2024 AIAA SciTech Forum [3, 4]. Previous assumptions about larger battery-electric aircraft were meticulously dismantled, cementing the small company’s place among aviation giants.
The Pertinent Parameters
Aircraft designers develop aircraft concepts of various sizes based on several key top-level requirements. Data from previous aircraft is used to make informed decisions for new designs. However, making sense of the interdependencies between these old concepts from just raw values of mass and dimensions is impractical. For this reason, designers prefer working with mass fractions to encapsulate the trends between aircraft of various sizes. The energy mass fraction, for example, expresses the ratio of the mass of the fuel source to the maximum take-off mass of the aircraft. The operational empty mass fraction captures the ratio between the structural mass of the aircraft and the maximum mass, and a similar inference can be made for the payload mass fraction. These fractions are extremely useful in the evaluation of new concepts.
Debunking Myths
Several research articles published in aeronautical journals discarded the feasibility of battery-electric aircraft for several reasons. One research article by Epstein and O’Flarity commented that the required shaft power and energy at take-off were too demanding for battery technology [5]. Another article by Viswanathan et al. commented that a fundamental reassessment of battery chemistry would be needed considering the gravimetric density of current batteries [6]. However, in the paper entitled, “A New Perspective on Battery-Electric Aviation, Part I: Reassessment of Achievable Range”, Elysian and its research partners at TU Delft re-evaluated these assumptions and performed a first estimate for range calculation [3].
Myth 1: The energy mass fraction required is simply too high
Research has suggested a causal correlation between the empty mass fraction and aircraft size, see Figure 1. Even though larger aircraft show a lower empty mass fraction of nearly 50% due to the positive scaling effects, battery technology is still considered too heavy to accommodate the energy mass fraction within the remaining total. The conclusion was that either the payload fraction must be sacrificed or exotic materials are needed to reduce the empty mass fraction, to provide enough capacity for the batteries [3].
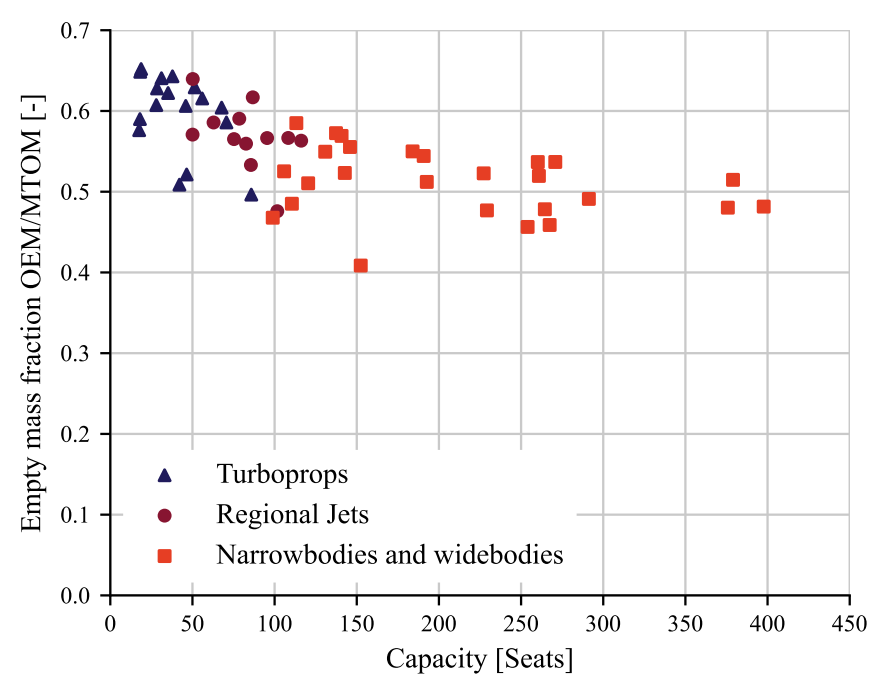
However, analyses by Obert and Torenbeek led to a different conclusion; the empty mass fraction was almost independent of aircraft size and more dependent on the range [7, 8]. Their analyses implied that larger aircraft do not have lower empty mass fractions due to the combination of lightweight structure and positive-scale effects, but rather have higher energy mass fractions due to their range requirements.
The trends uncovered by Elysian in their derivations supported this observation. Interestingly, the relationships between different mass fractions and the energy mass fraction held across all narrowbody aircraft, regardless of size, did not suggest a causal link between empty mass and aircraft dimensions as initially believed.
The consequence of this myth was the reassessment of reference aircraft for battery-electric technology. Unlike traditional short-range turboprops, which are efficient for their missions, battery-electric aircraft inherently have a higher energy mass fraction due to their heavier energy carriers and resemble first-generation jet models more than current fossil-fuel planes [3]. In other words, trying to replicate turboprops for battery-electric aircraft, as many were doing in the aerospace field, was inherently incorrect. The researchers concluded that a more appropriate reference for short-range battery-electric aircraft would be a 70-100-seat single-aisle fossil-fuel aircraft with an empty mass fraction below 45% [3].
Myth 2: Required aerodynamic performance is unattainable with current technology
Aerodynamic efficiency measures how much lift an aircraft can produce with drag as the price to pay; it contributes significantly to energy efficiency, which is particularly important for battery-electric aircraft considering the battery weight that has to be carried from origin to destination. To compensate for these heavier batteries, the aerodynamic efficiency of battery-electric aircraft would need to be much higher. However, such increases are believed to be attainable only by using technologies with a low Technology Readiness Level (TRL).
Over the years, the maximum aircraft aerodynamic efficiency has ranged between 14-18, see Figure 2. This efficiency inversely relates to the ratio of wetted area to wing reference area based on an estimate by Raymer [9]. The wetted area is the total surface area in contact with the external airflow, whereas the wing reference area is simply the planform area of the wings.
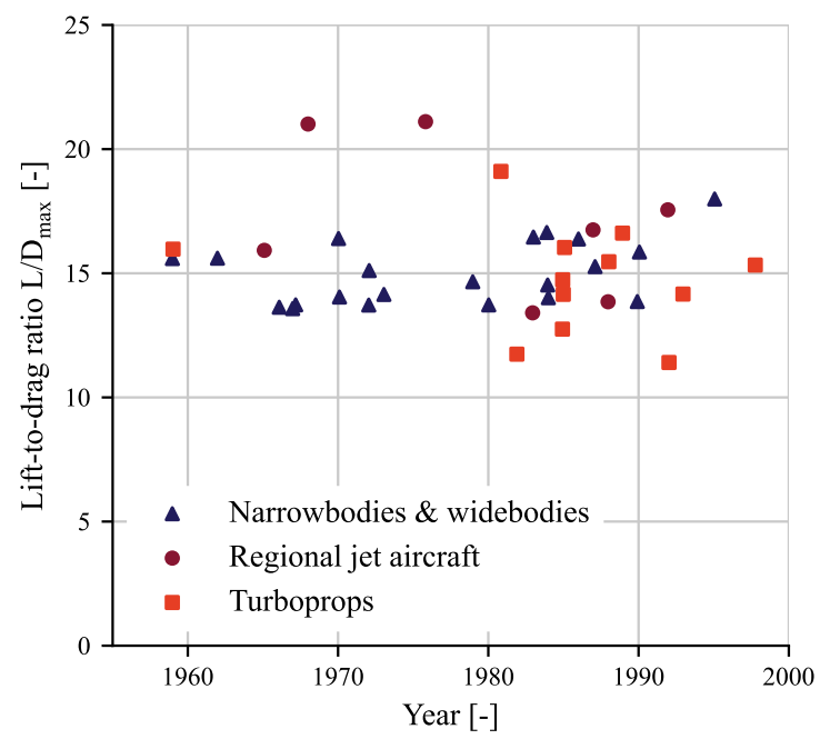
Elysian realized that for battery-electric aircraft to possess reasonable range capabilities – these planes must have high energy mass fractions, which results in a higher maximum aircraft mass, and bigger wings to lift the weight. The researchers justified the larger wings by stating that as the battery gravimetric density is almost twice that of current jet fuel, they can be stored within the wings to provide significant aerodynamic bending relief [3].
The researchers remarked that due to a larger wing, the aircraft would also require larger horizontal and vertical tail areas; however, these tail areas grow slower than the increase in wing area [3]. Therefore the ratio of wetted area to wing-reference area reduces, increasing the aerodynamic efficiency by up to three points – significantly higher than previously assumed. Note that this increase is a direct consequence of the wing sizing for a battery-electric aircraft and has nothing to do with new aerodynamic technologies, disproving the myth.
To account for the fact that the aerodynamic and propulsion characteristics of this aircraft type are so closely intertwined, the researchers introduced a new parameter into the research field, dubbed the Electric Range Factor (ERF) [3]. The ERF is simply a product of aerodynamic efficiency and the energy mass fraction, which proves extremely useful when determining the range for battery-electric aircraft and their parametric design.
Myth 3: Reserve requirements result in a practical range close to zero
EASA regulations require a specific amount of reserve fuel for emergencies and diversions [10]. Given that these reserves vary based on several operational factors and aircraft types, establishing a universal design requirement is challenging.
In practice, reserves are rarely used for diversions to alternate airports and final reserve usage is uncommon. In the spirit of saving weight, the researchers propose carrying reserve energy through a turbine-generator system running on Sustainable Aviation Fuel (SAF) rather than using batteries [3]. The researchers also note that even with a dual system, that could be required for redundancy and certification, the total mass would still be lighter than a battery system. Thus, the researchers assert that reserve requirements do not drastically limit operational range.
Myth 4: Battery-electric aircraft negatively scale with aircraft size
Several experts argue that battery-electric propulsion is only viable for small-scale aircraft, not larger transport aircraft, citing economic and technical reasons [11, 12]. The economic argument is that battery-electric aircraft can only serve low-range routes and, as a result, serve a small market. However, the researchers at Elysian argue otherwise in their paper, where range isn’t a limitation.
From a technical viewpoint, the researchers point to several arguments that counter the negative scale effects, where negative scaling refers to a decrease in aircraft performance due to an increase in size. Analysis by Torenbeek and Obert indicates that larger aircraft benefit from lower pilot and avionics mass fractions, thereby giving more capacity for other critical aircraft systems [7, 8]. Also, larger aircraft allow for greater battery storage capacity in the wing, offering structural and aerodynamic advantages.
The authors acknowledge that certain negative-scale factors do exist in terms of electric propulsors and their power-to-mass ratios. However, given that two motors and smaller propellers can offer better efficiency than a larger motor-propeller system, the authors point to a distributed propulsion configuration to counter this effect and show that larger electric aircraft are practical [3].
A Revised Range Estimate
The researchers performed Class-II mass and aerodynamic estimates to assess feasible ERF values on twelve parametric aircraft designs on passenger numbers between 40-120 and ERF values between 6-12. Their results concluded that a feasible maximum cruise range could reach values above 1000 km. Based on these estimates, passengers could fly from Amsterdam to Prague, New York to Toronto, or Los Angeles to San Francisco – with zero emissions [1]. Battery-electric aviation thus provides great opportunities to convert popular routes to green routes.
Designing the E9X
Motivated by their findings, Elysian went on to perform a conceptual design of a battery-electric aircraft and validate the findings of their first paper – extensively covered in the second paper, “A New Perspective on Battery-Electric Aviation, Part II: Conceptual Design of a 90-Seater” [4].
Most of the design choices in the E9X are related to minimizing the empty mass fraction of the aircraft. A unique feature of the design was the irregular proportions compared to existing narrowbodies such as the A320. The fuselage of the E9X is significantly smaller as it carries almost half the passengers. However, the wing is considerably larger as a function of the aerodynamics of such an aircraft (figure 3).
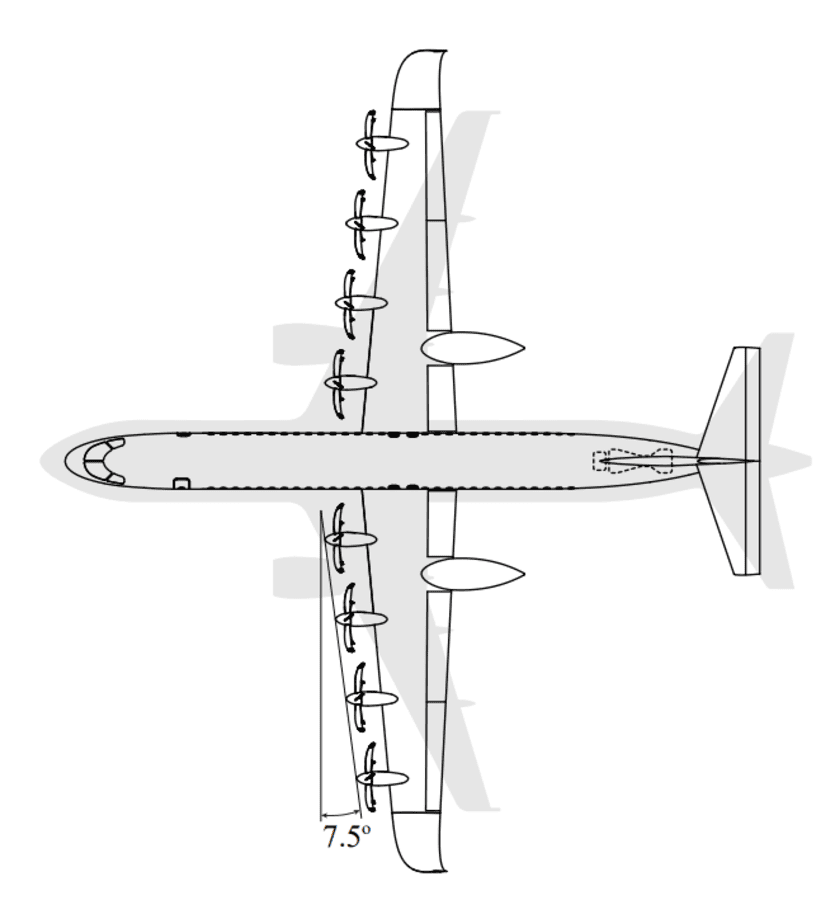
For the wing design, several configurational choices were made for weight reduction. Batteries are stored in the wings, relieving the aerodynamic bending loads and facilitating a lighter structure. However, battery integration and packaging for replacement and inspection are challenges that would have to be addressed [4]. Safety mechanisms for battery failure are another area needing consideration. In terms of positioning, a low-wing configuration was chosen for a shorter and hence lighter main landing gear.
The aspect ratio of an aircraft represents the ratio of the wingspan to the wing chord. A higher aspect ratio for an aircraft weakens tip vortices, reducing drag and increasing aerodynamic efficiency. However, for the E9X, a modest aspect ratio was chosen to provide more wing volume for powertrain components and diminish aeroelastic effects [4]. Despite the modesty, the wingspan exceeds the gate-span limits, and the researchers propose a folding wing-tips solution similar to the Boeing 777X (figure 4). Another distinctive design element is storing the main landing gear within the wing itself, primarily due to the smaller fuselage.
The E9X also has eight propellers covering the entirety of the wing span utilizing a direct-drive arrangement for simplicity, see Figure 3. The aircraft has a particularly low disk loading compared to typical turboprop aircraft (377N/m2 compared to 500-800N/m2 ) that ensures a high propeller efficiency in cruise and especially during take-off, which is important for motor power and sizing.
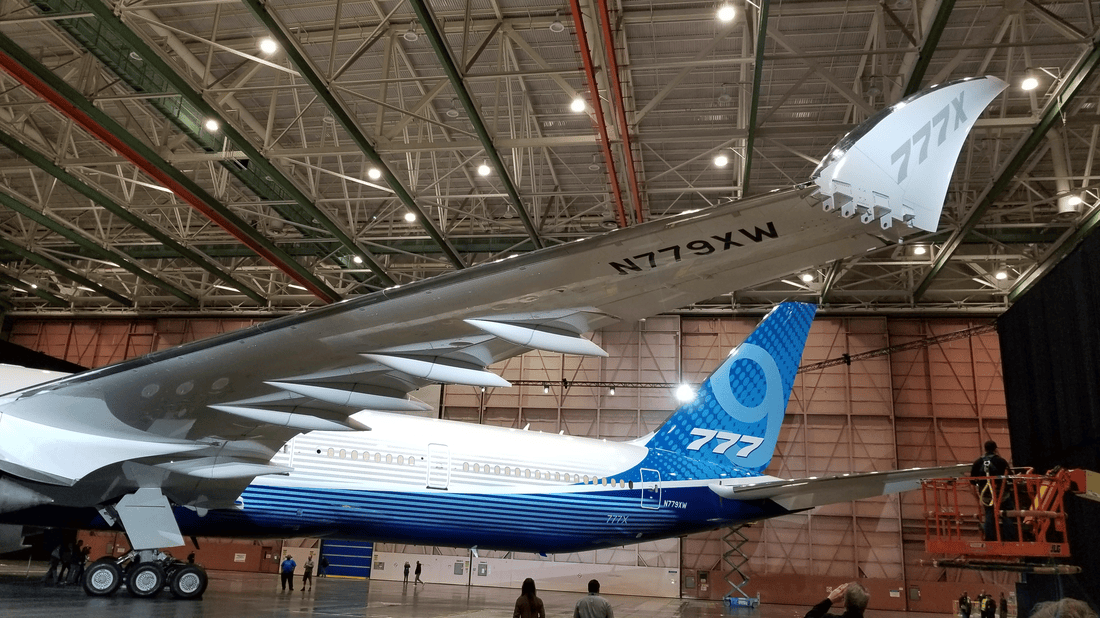
Environmental Impact
The primary purpose of Elysian’s project is to provide a superior sustainable option compared to other current and promising future propulsion technologies, which include liquid hydrogen and eSAF [4]. To fairly evaluate these technologies for environmental impact, well-to-tank (grid) and tank-to-wake (vehicle) energy consumption per passenger-kilometer are evaluated for all propulsion technologies.
In terms of tank-to-wake, the researchers evaluate energy consumption per passenger-kilometer for various transport modes over an 800 km range, a conservative mission range for a 1st generation electric aircraft designed to carry 90 passengers [4]. This analysis includes comparisons with a next-gen turboprop, an A320neo-like narrowbody, and hydrogen-fuel concepts. And also ground transportation options like electric cars and trains. The findings shown in Figure 5 reveal that the battery-electric aircraft (167 Wh/pax-km) and the conventional turboprop (187 Wh/pax-km) are nearly comparable in energy consumption. Despite being over twice as heavy, the electric aircraft benefits from higher efficiency, contributing to its competitive energy profile.
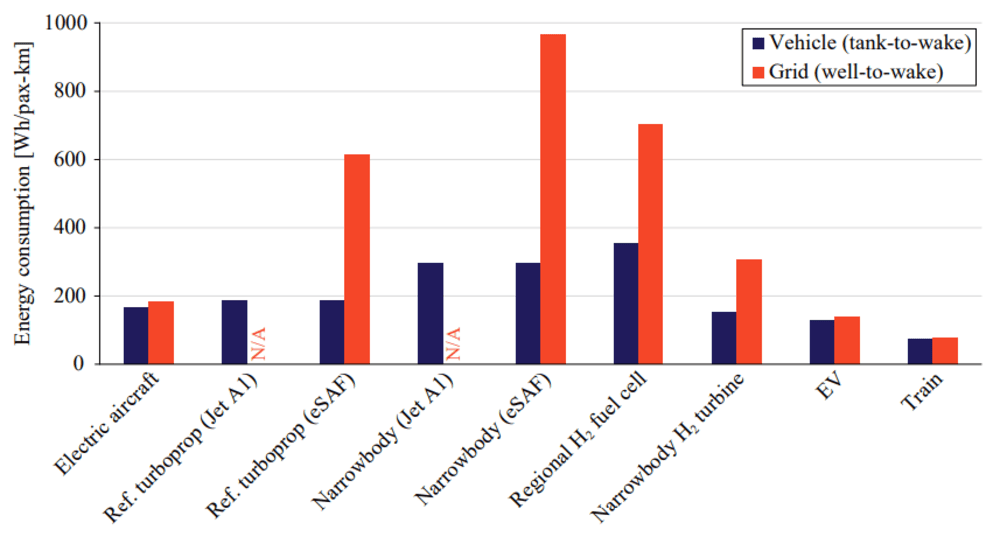
Efficiency from the grid to the propulsor system plays a crucial role in assessing these pathways. For instance, it takes about 1.3 kWh of grid energy to produce 1 kWh of usable power for battery-electric aircraft, whereas hydrogen turbine and fuel cell options require approximately 4 kWh, and eSAF demands 5-9 kWh. This shows that battery-electric systems are roughly three to six times more efficient than hydrogen or eSAF options [4]. This efficiency is particularly important when examining grid energy use—an indicator of life-cycle emissions. Battery-electric aircraft still demonstrate impressive efficiency, requiring approximately 70-80% less grid energy than eSAF aircraft and 40-75% less than hydrogen counterparts. The electric aircraft’s energy consumption aligns closely with ground-based electric vehicles and is about twice that of trains per passenger-kilometer [4].
Elysian also compares the CO2-equivalent emissions per passenger-kilometer of different transport modes, highlighting the environmental impact of future aircraft technologies. The report considers emissions from in-flight CO2 and non-CO2 effects, energy production, and battery manufacturing but excludes vehicle and infrastructure manufacturing [4]. Non-CO2 effects include contrail formation and NOx production [13]. It shows that battery-electric aircraft, powered by a future grid mix with high renewables equating to 114gCO2/kWh (Europe’s 2030 target) [14], are significantly cleaner than hydrogen or kerosene-powered planes for short missions (figure 6).
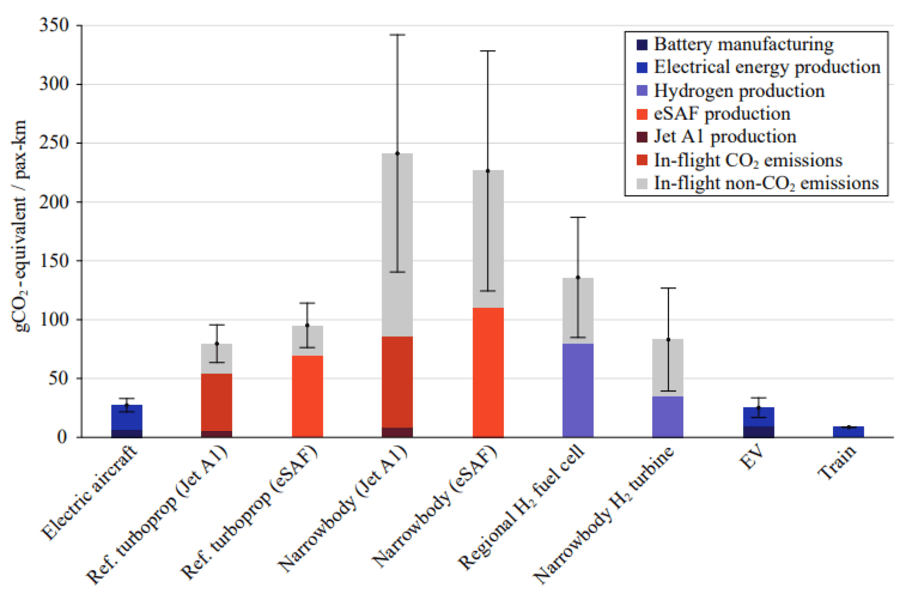
SAF offers short-term emission reductions due to its ease of implementation. However, its long-term viability hinges on a fully renewable energy grid, as other energy sources would have been developed and inherently have lesser emissions, as shown in Figure 7. Current SAF technologies like biofuels are limited in scalability, and synthetic fuels require abundant green energy and are inadequate long-term solutions. Hydrogen aircraft, although promising, currently have higher CO2-equivalent emissions due to their heavier airframes and non-CO2 effects [4].
Battery-electric aircraft are found to have a similar environmental impact as electric cars and trains on a per-passenger basis. This suggests that, if feasible, short-haul flights should prioritize electric propulsion over fuel-based alternatives, as it presents a clear advantage in reducing emissions [4]. The analysis also highlights that while electric aircraft could make short-haul flight bans, like those in France, unnecessary, hydrogen and eSAF are better suited for longer-range missions where batteries fall short.
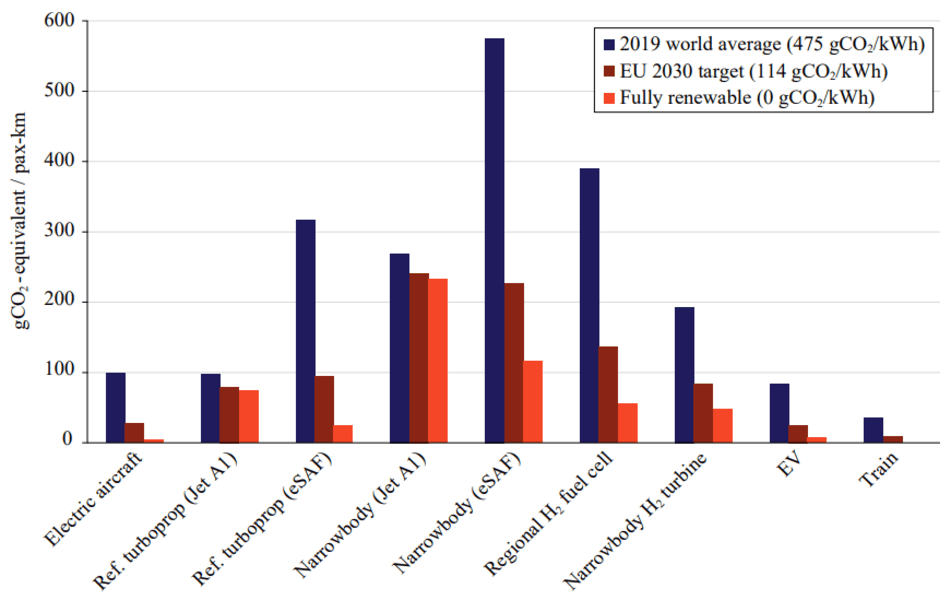
The Future
Elysian has bold ambitions to launch its E9X variant by 2033, introducing itself as a game-changer for the aviation industry. The company plans to finish the final stages of conceptual design by 2025, after which they plan on moving to preliminary design, system testing and aircraft certification. With the support of several industry partners such as NLR, Fokker, and DLR as well as an experienced and accomplished supervisory board, Elysian looks to grow strong in the years to come.
Conclusion
This article provided a look back into the origins of Elysian, a company still in its juvenile stage. Several myths about battery-electric aircraft were debunked by their researchers, and the E9X was developed as a proof-of-concept. Elysian’s aircraft offers a significant opportunity to achieve net-zero carbon emission targets by serving several air-travel routes within the EU and North America. For students, engineers, and executives who deal with vast amounts of data, research and engineering processes on an almost daily basis, Elysian offers a stark reminder that we must be critical yet open-minded to the possibilities and opportunities for future technologies presented to us; “Correlation does not imply causation”, and to truly make a change, we must innovate and not replicate.
References
[1] Elysian Aircraft (2024, October 12). Elysian Aircraft. elysianaircraft.com
[2] A route to net zero European aviation. (2024, October 12) Destination 2050. destination2050.eu
[3] Wolleswinkel, R. E., de Vries, R., Hoogreef, M. F. M., & Vos, R. (2024). A New Perspective on BatteryElectric Aviation, Part I: Reassessment of Achievable Range. In Proceedings of the AIAA SciTech 2024 Forum Article AIAA 2024-1489 (AIAA SciTech Forum and Exposition, 2024). American Institute of Aeronautics and Astronautics. https://doi.org/10.2514/6.2024-1489
[4] de Vries, R., Wolleswinkel, R. E., Hoogreef, M. F. M., & Vos, R. (2024). A New Perspective on BatteryElectric Aviation, Part II: Conceptual Design of a 90-Seater. In Proceedings of the AIAA SciTech 2024 Forum Article AIAA 2024-1490 (AIAA SciTech Forum and Exposition, 2024). American Institute of Aeronautics and Astronautics. https://doi.org/10.2514/6.2024-1490
[5] Epstein, A. H., & O’Flarity, S. M. (2019). Considerations for Reducing Aviation’s CO2 with Aircraft Electric Propulsion. Journal of Propulsion and Power, 35(3), 572–582. https://doi.org/10.2514/1.b37015
[6] Viswanathan, V., Epstein, A. H., Chiang, Y. M., Takeuchi, E., Bradley, M., Langford, J., & Winter, M. (2022). The challenges and opportunities of battery-powered flight. Nature, 601(7894), 519–525. https://doi.org/10.1038/s41586-021-04139-1
[7] Obert, E. (2009). Aerodynamic design of transport aircraft. IOS Press.
[8] Torenbeek, E. (2013). Advanced Aircraft Design – Conceptual Design, Analysis and Optimization of Subsonic Civil Airplanes. John Wiley & Sons.
[9] Raymer, D. (2018). Aircraft Design: A Conceptual Approach, Sixth edition. https://doi.org/10.2514/4.104909
[10] de Moor, S. (2024, October 12). Navigating and Understanding EASA’s Latest Fuel/Energy Scheme Requirements. Honeywell. aerospace.honeywell.com
[11] Webber, H., & Job, S. (2021). Realizing Zero-Carbon Emission Flight. Aerospace Technology Institute report. ati.org.uk
[12] Waypoint 2050 – Balancing growth in connectivity with a comprehensive global air transport response to the climate emergency: a vision of net-zero aviation by mid-century. (2021). Air Transport Action Group. atag.org
[13] Non-CO2 Emissions – Contrails. (2024, October 12). American Institute of Aeronautics and Astronautics. iata.org
[14] Greenhouse gas emission intensity of electricity generation in Europe. (2024, October 12). European Environment Agency. eea.europa.eu